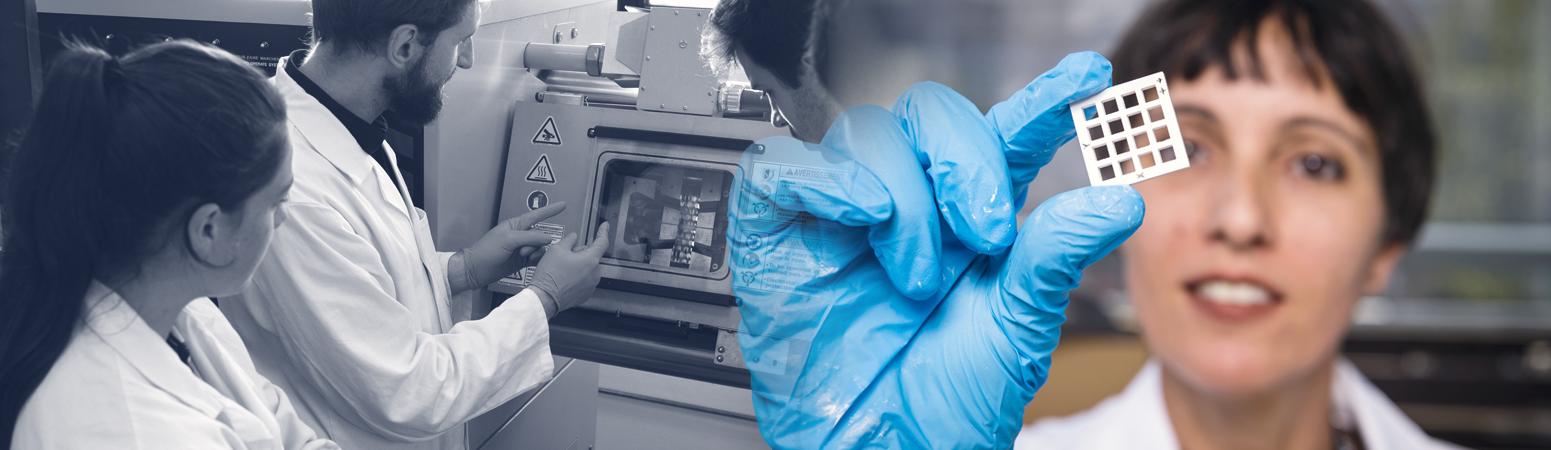
Teams
The METAL group uses and develops several types of simulations in order to investigate the microstructural evolution, plastic deformation and failure of materials through a multi-scale modeling approach. At the atomic and nano scales, we use atomistic simulations and kinetic Monter-Carlo simulations to investigate small-scale plasticity processes in metals, oxydes and amorphous materials (e.g., glass and polymers). Plasticity is also investigated using methods as Discrete Dislocation Dynamics (DDD) up to the macroscopic scale including Finite-Elements methods (FEM). Still at the macro-scale, 2D and 3D experiments are used to explore the deformation and fracture of metals and alloys in polycrystalline simulations using reallistic sample.
DISLOCATIONS AND NANOMECHANICS
contact: Dr. Jonathan Amodeo, Pr. Michel Perez
The deformation of crystalline solids is due to complex processes controlled by dislocations. Owing to the characteristic sizes of such defects, molecular dynamics (MD) simulations have revealed to give valuable pieces of information regarding deformation mechanisms. Several topics are investigated in the METAL group as nanocompression and nanoindentation modeling (Fig. 1b), dislocations in irradiated materials and intermetallics, Cotrell atmosphere formation (Fig. 1a) or dislocation vs. interfaces (surfaces, GBs, twin boundaries) interactions. Among other, the mechanical properties of nano-objects such as pillars, particles or wires have recently drawn intensive scientific attention, mainly through their high achievable yield strength and ductility. This size effect involves both the elastic and the plastic deformation regime for whom dislocation nucleation and twinning become the main mechanisms responsible for strengthening ("smaller is stronger”). The METAL group uses MD and DDD simulations to perform virtual nano-compression tests and investigate small-scale mechanical properties of crystalline materials. Generally, these simulations allow a better understanding of the deformation mechanisms and are at the basis of a theoretical underpinning which are crucial to interpret in situ TEM tests performed at the MATEIS laboratory.
(a) (b)
Fig. 1 (a) Evolution of carbon atoms around screw and edge dislocations in iron computed using MD and statistical approaches (Vega et al. J. Phys.: Condens. Matter. 2013). (b) MD simulation of the compression of an Ni3Al nanocube. One can see the nucleation of partial dislocations (atoms in red belong to stacking fault environment) from the surface of the nanocube as the main mechanism during the first steps fo the deformation (Amodeo et al. Materials Research Letters 2014).
DISLOCATION DYNAMICS AND CRYSTAL PLASTICITY
contact: Dr. Jonathan Amodeo, Dr. Sylvain Dancette
The METAL group investigates the plastic deformation of materials using Dislocation Dynamics (DD) simulation and crystal plasticity modeling. DD simulations illustrate the collective behaviour of dislocations at the grain scale and allow to study e.g., dislocation interactions (Fig. 2a), the generation of dislocation microstructures or to compute hardening coefficients which are key parameters required in larger scale simulations. This research field is developped in collaboration with Dr. Benoit Devincre (LEM, Chatilllon) using the microMegas DD code. In the METAL group, DD simulations are part of a multi-scale modeling approach as these simulations generally integrate parameters (elastic constants, dislocation mobility law, activation parameters) computed at lowe scale using e.g., atomistic simulations, and are often designed to feed macroscopic models. To do so, crystal plasticity simulations (often used together FEM methods) are used to reach new space and time scales (Fig. 2b), especially allowing larger deformation ranges and polycrystalline simulations. This field is developped in collaboration with Laurent Delannay (UCL, Louvain-La-Neuve).
(a) (b)
Fig. 2 (a) Dislocation (in red) gliding and interacting with other defects modeled by Dislocation Dynamics. Eight consecutive (and superimposed) snapshots are represented (Amodeo et al. Mechanics of Materials 2014). (b) Polycrystal deformed using atomistically-informed finite-element crystal plasticity simulations (Amodeo et al. International Journal of Plasticity 2016).
PRECIPITATION AND MICROSTRUCTURE MODELING
contact: Pr. Michel Perez
Thermo-mechanical treatments used to design and optimise the microstructure of metals lead to more and more complex microstructures. A mean field precipitation model, based on classical nucleation and growth theories, was developed in the METAL group. It is implemented in an open source software: PreciSo. In parallel, other phase transformation models have been developed (e.g. ferrite to austenite transformation) in the group. The aim of these models is to produce microstructural data as input parameter for models predicting other microstructural features (e.g. grain size) and/or mechanical properties. Furthermore, results from these models are used to build physically based constitutive laws for FEM simulations i.e., the main idea it to couple models predicting microstructural features (e.g. precipitation, grain size, solute content, dislocation density) to mean field models describing yield stress and hardening (e.g. Kocks-Meching-Estrin). Collaborators for this topic are Dr. Thibaut Chaise, Pr. Daniel Nelias (LaMCoS, Lyon, Lyon) and Pr. Alexis Deschamps (SIMAP, Grenoble).
Fig. 3 Modelled TTT diagram and associated yield stress in a 718 super alloy (Ph.D A. Balan)
EXPERIMENTALLY-INFORMED FINITE-ELEMENT MODELING
contact: Dr. Sylvain Dancette, Dr. Eric Maire
The METAL group investigates the mechanical behaviour of metallic alloys using FEM simulations based on the realistic microstructural observations in 2D (optical microscopy, SEM, EBSD) and 3D (absorption and diffraction contrast tomography) performed at the MATEIS laboratory. This topic focus on (i) developping tools to manipulate and optimize 2D and 3D meshing of experimental sample, (ii) developping deformation and failure models at different scales and (iii) the cohenrecy between modeling and experimental approaches.
Fig. 4 Global calculation of a stainless steel metal hollow sphere structure sample (Caty et al. Acta Materialia 2008).
MECHANICAL PROPERTIES OF AMORPHOUS MATERIALS
contact: Pr. Michel Perez, Pr. Patrice Chantrenne, Dr. Julien Morthomas
Metallic or not, amorphous materials are the subject of many fundamental studies in the Metal Group. The main topic of these studies is the relationship between microstructure at the atomic scale and mechanical properties. Molecular dynamics is a technique of choice since the microstructure can be fully controlled. In this field, Molecular Dynamics is used as a predictive tools, but mostly for testing ideas. This topic includes collaborations at MATEIS (Pr. Olivier Lame, Pr. Laurent Chazeau, Pr. Karine Masenelli-Varlot) and at SIMAP (Dr. Christophe Martin).
Fig. 5 Silica aerogel studied by molecular dynamics (Ph.D W. Goncalvez)