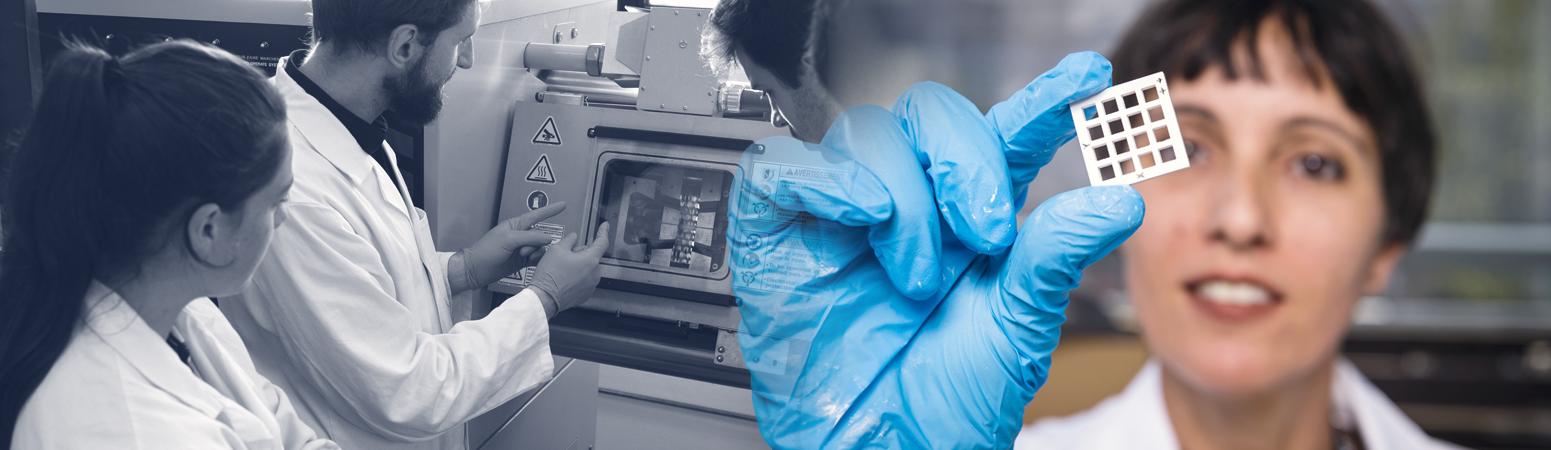
Teams
The METAL group investigates the mechanical properties of metals and composite materials under monotonous or cyclic loading using several methods of analysis as X-ray tomography, microscopy and acoustic emission.
MONOTONOUS MECHANICAL TESTING
contact: Dr. Eric Maire
Mechanical tests under monotonous loading are developped to investigate plastic deformation, mechanical embrittlement and failure under an continously increasing load. The METAL group performs classical tensile and compression tests using its own testing machines generally coupling mechanical tests and in situ observations using e.g. TEM or tomography analysis. On this topic, a specific attention is paid to the fracture of materials. The macroscopic fail of a metal happens after the occurence of micro-cracks and micro-cavities which are signs of mechanical embrittlement at the microscopic scale. These damages begin, grow and coalesce leading to the material macroscopic failure. The quantification of these three phases has recently made significant progresses largely due to 3D in situ observations. To encourage these observations, the METAL group fabricates composite model materials in which the simplified microstructure resolve classical ambiguities responsible for observation disturbances. One example is the recent work of Ferre and coworkers on the embrittlement of aluminum-based composite materials which is strengthened by amorphous spherical inclusions.
Fig. 1 Damage evolution in an aluminum-based composite materials including amorphous spherical inclusions observed by X-ray tomography (ESRF, ID19). (Ferre et al. Materials Science and Technology 2015).
CYCLIC MECHANICAL TESTING
contact: Pr. Jean-Yves Buffière
Since 2000, the METAL group has gained a large experience in the field of 3D characterisation of damage under cyclic loading. Several experimental setups have been designed to apply stress under cyclic conditions into the tomograph and investigate in situ crack nucleation and propagation with a spatial resolution of few micrometers. These tests can be carried out at the MATEIS laboratory or at synchrotron facilities. As an example, damage in cast iron made of nodular graphites that shows a natural microstructural pattern has been investigated at the lab. Nevertheless, the use of a synchrotron beam allows to used bigger machines for which the detector-to-sample distance is not restricted. Setups including constant amplitude cyclic load have been developped to investigate damages development in various metals and structural alloys using uni-axial or torsion cyclic loading. The crack propagation in cast aluminum alloys has been investigated for the first time at high temperature (250°C) (see Fig. 2). Furthermore, mechanical tests together with DCT measurements have allowed to study crack propagation path in polycrystals (Fig. 3).
Fig. 2 Observation of a crack propagation during cyclic loading at 250°C in cast aluminum alloy used for the automotive industry (Dezecot et al. Acta Materialia 2016).
Fig. 3 in situ observation of crack propagation in a titanium alloy (Herbig et al. Acta Materialia 2011)
2D AND 3D CHARACTERIZATION
contact: Dr. Sophie Cazottes, Dr. Jérôme Adrien, Dr. Wolfgang Ludwig
The METAL group and the MATEIS laboratory benefit of a large set of deformation characterization tools that can be used in situ at several space scales. A the micrometer scale, the METAL group has an in situ setup that allows to perform tension and 3/4-points flexure mechanical tests inside the SEM. This setup can also be used for deformation monitoring inside the optical microscope. Thus, we are able to characterize the deformation state at the grain scale using EBSD (see Fig. 4a) and to further use these data together with crystal plasticity models to better understand the behaviour of the different phases inside the alloy.
In addition to these techniques, the METAL group develops important capabilities in the field of non-destructive 3D characterization of materials (see Fig. 4b). The group has two lab X-ray tomographs which reach a wide set of resolution i.e., from few hundreds of nanometers to micrometers. Several setups have been developped to investigate materials under stress. Many field trials are done at the synchtrotron (ESRF, SOLEIL or SLS) when better resolutions are required. Also, these facilities enable the use of diffraction contrast 3D tomography (DCT).
Fig. 4 (a) EBSD Maps of a duplex steel revealing ferrite grains rotation, and deformation localisation during in situ tensile tests performed in the SEM (courtesy Dr. S. Cazottes), (b) 3D morphological analysis of copper foams as current collectors for Li-ion batteries by means of X-ray tomography (A. Etiemble et al. Mater. Sci. Eng., B 2014).
CARACTERIZATION USING ACOUSTIC EMISSION
contact: Dr. Stéphanie Deschanel
The METAL group and the MATEIS laboratory have a strong expertise in the development of acoustic emission (AE) measurements and data analysis in a wide range of experiments for several materials. AE is probably one of the most powerful and versatile non-destructive tools to analyze dynamic instabilities involving topological defects, such as dislocation avalanches, twinning, phase transformations and microcracking. AE records the elastic waves generated by the rapid inelastic deformations associated to these instabilities. Using appropriate AE source models, the characteristics of the wave (amplitude, energy, duration, frequency) are related to the characteristics of the source (e.g., to the micro-crack size, to the strain increment due to the dislocation avalanche, or to the advance of a phase boundary). By using AE sensor networks (see Fig. 5), one can monitor the distribution of the internal instabilities in space, time and energy domains. The time resolution is excellent (10-7s) and the energy range that can be explored is typically of several orders of magnitude. AE source locations can be determined from multiple sensors analysis. Defects of different nature can be distinguished from their AE signatures by using pattern recognition analysis. For instance, AE has been used in the context of fatigue to track individual defects and to monitor global damage activity.
Fig. 5 PCI2 Mistras data acquisition system of European Physical Acoustic (EPA) with a 8MHz sample rate and a 20/40/60 dB pre-amplification. Wide range of piezoelectric sensors (courtesy Dr. S. Deschanel).