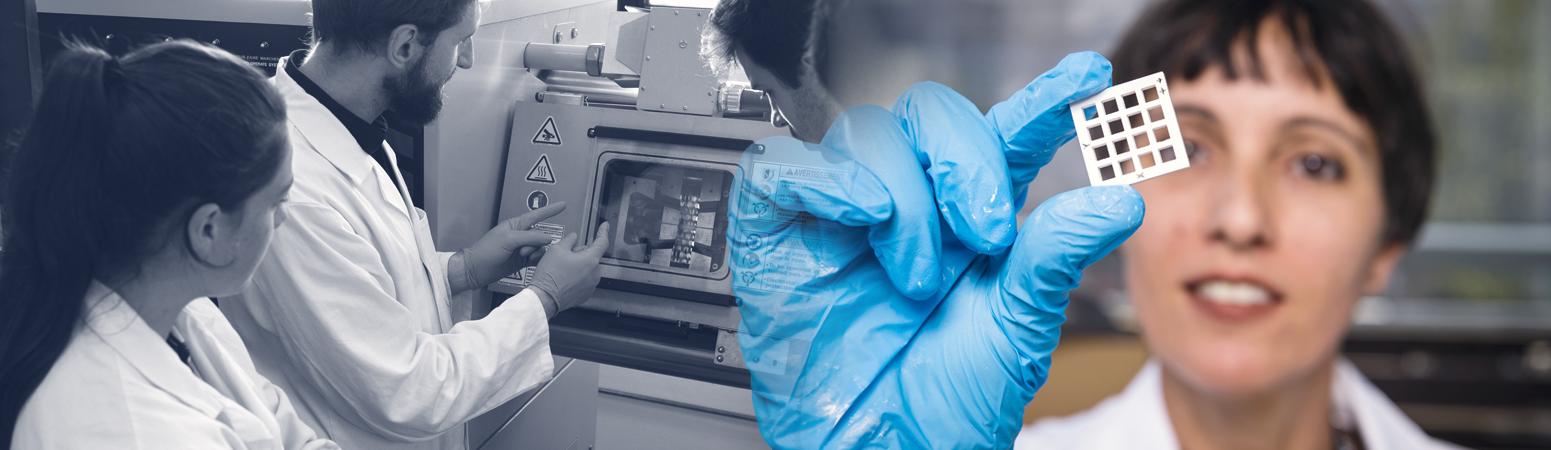
Teams
The METAL group develops innovating materials using powder metallurgy (spark plasma sintering) and is also renowned for the design of both architectured and porous materials.
ODS STEELS
contact: Pr. Damien Fabrègue, Dr. Xavier Boulnat
The fabrication of oxide-dispersion strengthened (ODS) steels is an important part of the work done in the METAL group in the field of materials design. These studies are often done in collaboration with The French Alternative Energies and Atomic Energy Commission (CEA). The goal is to make steels wich bear a dispersion of yttrium oxydes of few nanometers diameter, using powder metallurgy. These oxydes allow a high-temperature and long-time stable microstructure. One route to fabricate ODS steels is to mill steel and yttrium oxydes powders together (mechanical alloying) and then to apply a specific sintering cycle (a Joule-effect-based sintering called Spark Plasma Sintering) in order to maintain the particles and the microstructure as fine as possible. ODS steels have improved high-temperature creep properties, which is crucial in the field of nuclear materials applications.
Fig. 1 EBSD map of an ODS steel made using Spark Plasma Sintering (Mouawad et al. Journal of Nuclear Materials 2015).
METAL MATRIX COMPOSITE MATERIALS
contact: Dr. Eric Maire, Dr. Sylvain Dancette, Dr. Christophe Le Bourlot
The METAL group synthetizes model composite materials. These materials are based on a metallic matrix (e.g., aluminum) with a voluntary simplified inclusion-based microstructure made to easily measure stress and observe damage processes. As for ODS steels, these composites materials are made out of a powder metallurgy process i.e., they are pressed at low temperature while their extrusion is performed at high temperature to increase the ductility of the metallic matrix. Recent samples have been processed to test the strengthening capability of metallic glass inclusions (Ferre et al. Materials Science and Technology 2015). While in their bulk shape these amorphous materials (zirconium in this case) are reknown for their high strength and low ductility, their inclusion counterpart shows a surprising high ductility that enhances the composite mechanical properties.
Fig. 2 3D-imaging of a composite material fabricated using inadequate sintering conditions. A supplementary stage of extrusion at high temperature enhance the fabrication process reducing the porosities what leads to better mechanical properties. (Ferre et al. Materials Science and Technology 2015).
POROUS AND ARCHITECTURED MATERIALS
contact: Dr. Eric Maire, Pr. Damien Fabrègue, Dr. Xavier Boulnat
The METAL group fabricates architectured porous materials i.e., we make entangled metallic wires and crumple foils, both materials being shaped by cold-compaction inside cylindrical moulds. The group compares the mechanical properties of these two types of cheap and easy-to-make architectured materials. Quite surprisingly, these materials show reproducible mechanical properties which depends solely on the volumic fraction. In situ compression tests using X-ray tomography are performed to investigate the properties of such complex structures.
Fig. 3 3-D volume snapshots during in situ compression at different material volume fractions: (a) 9%, (b) 14%, (c) 20% and (d) 29%. (Cottrino et al. Acta Materialia 2014)